Manufacturing executives face a brutal reality today. Production lines that worked perfectly for decades now struggle against global competition, rising costs, and demanding customers who expect faster delivery, higher quality, and lower prices. The old ways of running a factory floor – relying on gut instinct, scheduled maintenance, and manual quality checks – simply don’t cut it anymore.
Smart manufacturers know the answer lies in artificial intelligence, but here’s the problem: implementing AI in manufacturing isn’t like installing new software on your laptop. You’re dealing with complex production systems, legacy equipment that’s been running since the Clinton administration, and workers who’ve been doing things the same way for twenty years. One wrong move and you could shut down your entire operation, costing millions in lost production.
That’s where specialized AI consulting firms come in. These aren’t your typical tech consultants who’ve never set foot on a factory floor. We’re talking about teams that understand the difference between theoretical AI applications and real-world manufacturing challenges. They know how to integrate machine learning algorithms with PLCs, implement computer vision systems that actually work in dusty industrial environments, and build predictive maintenance models that prevent costly downtime.
Companies Featured in This Analysis:
- Pearl Lemon AI
- Qubika
- Krazimo AI
- Root Quotient
- Simform
- Agile Cyber
- WillowTree Apps
- Intermedia IT
- Streaver
- Code Ninja Consulting
1. Pearl Lemon AI

When it comes to manufacturing AI implementations that actually deliver ROI, we’ve built our reputation on results, not promises. While other consulting firms talk about digital transformation, we focus on solving the specific problems that keep manufacturing executives awake at night: unplanned downtime, quality defects, inventory optimization, and production scheduling inefficiencies.
Our approach starts with understanding your existing manufacturing execution systems (MES), enterprise resource planning (ERP) infrastructure, and shop floor data architecture. We don’t believe in rip-and-replace strategies that disrupt production. Instead, we build AI solutions that integrate seamlessly with your current SCADA systems, historians, and programmable logic controllers (PLCs).
Our Core Manufacturing AI Services:
- Predictive maintenance algorithms for rotating equipment and production machinery
- Computer vision quality inspection systems for automated defect detection
- Supply chain optimization using machine learning demand forecasting
- Production scheduling AI that balances throughput, energy costs, and resource allocation
- Digital twin development for process optimization and scenario planning
- Industrial IoT sensor integration and edge computing deployment
- Manufacturing data lake architecture and real-time analytics platforms
What sets us apart is our understanding of manufacturing constraints that academic AI researchers never encounter. We know that your production data might be incomplete, inconsistent, or stored in proprietary formats. Our solutions are built for the reality of manufacturing, not the sanitized environment of a research lab.
2. Qubika
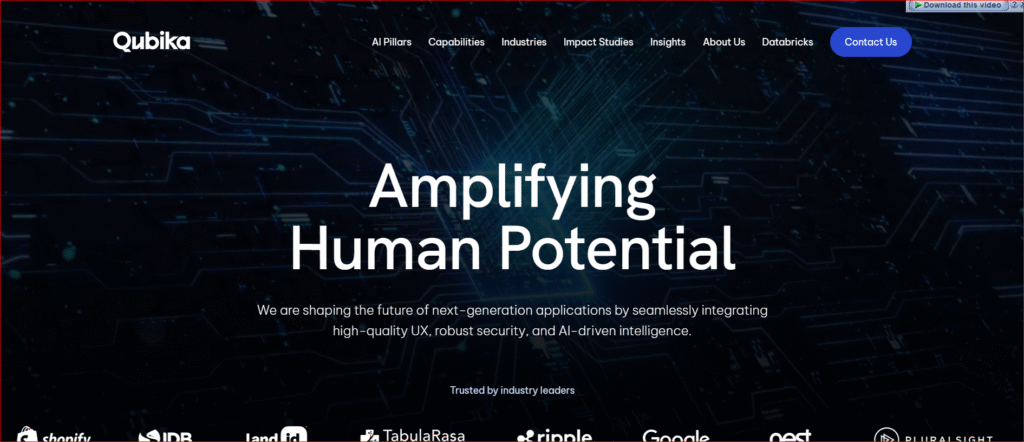
Qubika has carved out a strong position in the manufacturing AI space by focusing on end-to-end digital transformation projects rather than point solutions. Their approach centers on creating what they call “intelligent manufacturing ecosystems” – integrated platforms that connect everything from procurement systems to customer delivery tracking.
Their manufacturing practice combines traditional systems integration expertise with modern AI capabilities. Qubika’s teams understand the complexities of integrating new AI systems with legacy manufacturing equipment, particularly in facilities where some machinery might be running on protocols that predate the internet. They’ve developed specialized middleware solutions that bridge the gap between modern cloud-based AI platforms and industrial equipment using older protocols like Modbus or DeviceNet.
3. Krazimo AI
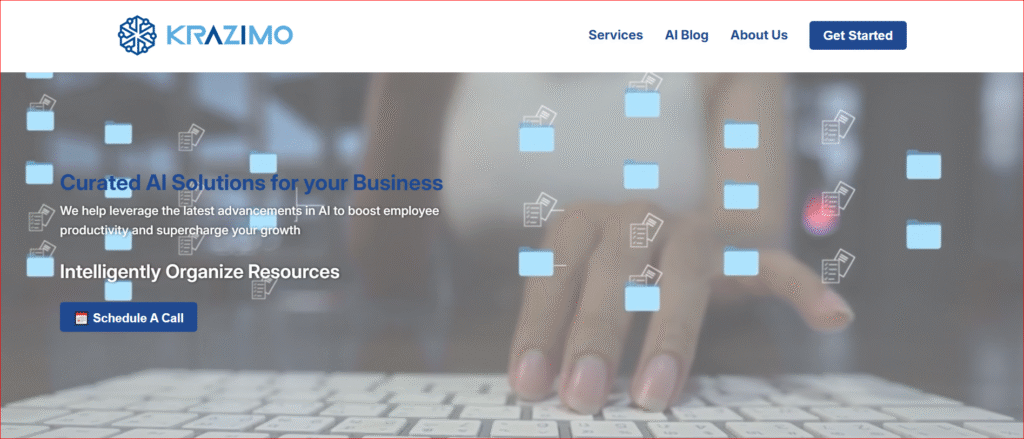
Krazimo AI has built their reputation around solving specific manufacturing challenges using advanced machine learning techniques. Rather than positioning themselves as generalist consultants, they focus on areas where AI can deliver measurable impact: predictive maintenance, quality assurance, and production optimization.
Their predictive maintenance solutions go beyond simple vibration monitoring or temperature tracking. Krazimo’s systems integrate multiple data sources – including acoustic analysis, thermal imaging, electrical signature analysis, and process parameters – to create comprehensive equipment health models. They understand that effective predictive maintenance requires predicting failure modes, estimating remaining useful life, and providing actionable maintenance recommendations that fit within production schedules.
4. Root Quotient
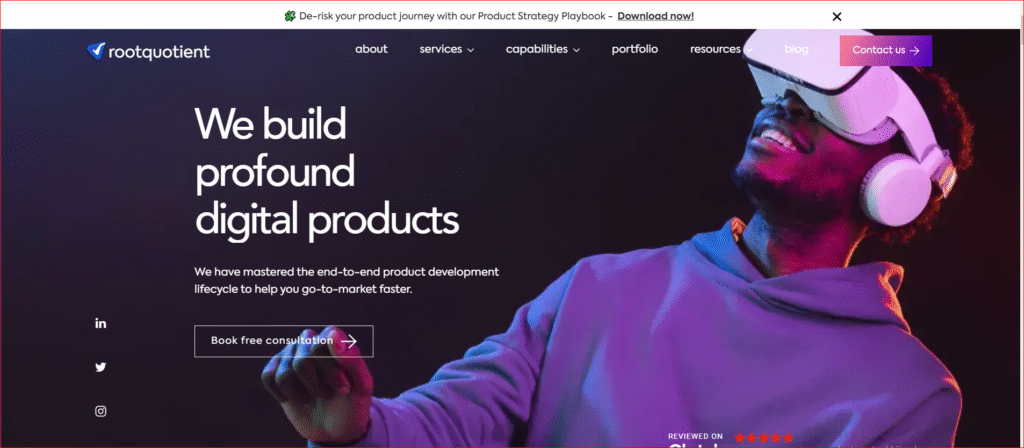
Root Quotient takes a data-first approach to manufacturing AI, recognizing that most manufacturing organizations have valuable data trapped in silos throughout their operations. Their methodology starts with comprehensive data audits to identify all available information sources – from ERP systems and quality databases to maintenance logs and operator notes.
Their team includes data scientists with specific experience in manufacturing environments who understand the unique challenges of working with industrial data. Manufacturing data often comes with complications: sensor readings that drift over time, measurements taken under varying environmental conditions, and data collection systems that experience interruptions. Root Quotient’s preprocessing techniques are specifically designed to handle these manufacturing-specific data quality issues.
5. Simform
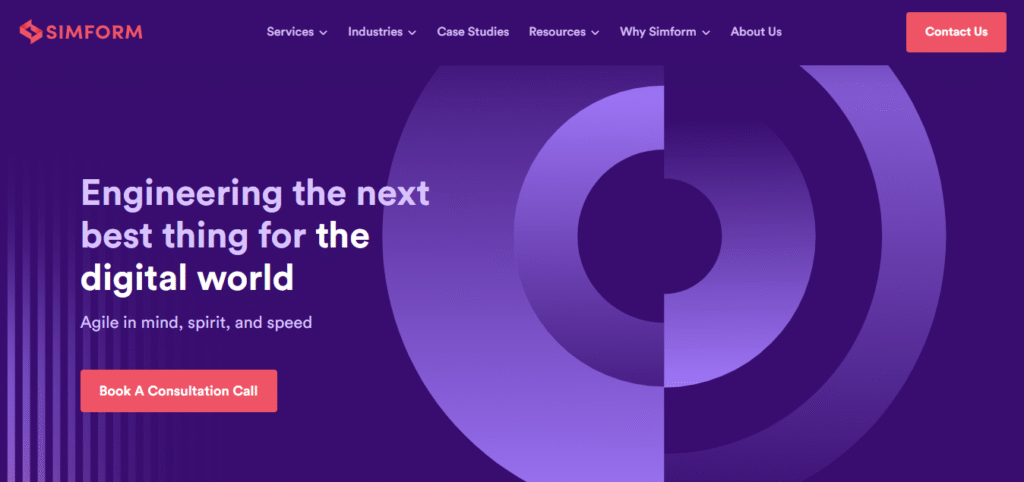
Simform brings a software development company’s perspective to manufacturing AI, which proves valuable for building robust, scalable AI applications that handle high-volume data streams common in modern manufacturing operations. They excel at creating user interfaces and dashboards that make complex AI insights accessible to plant managers and operators.
Their manufacturing AI solutions emphasize real-time processing and edge computing capabilities. Simform understands that many manufacturing AI applications can’t rely on cloud connectivity due to latency requirements or network reliability issues. Their edge computing platforms run AI algorithms locally on the factory floor, processing sensor data in real-time without depending on internet connectivity. This approach proves particularly valuable for real-time quality control or safety monitoring applications.
6. Agile Cyber
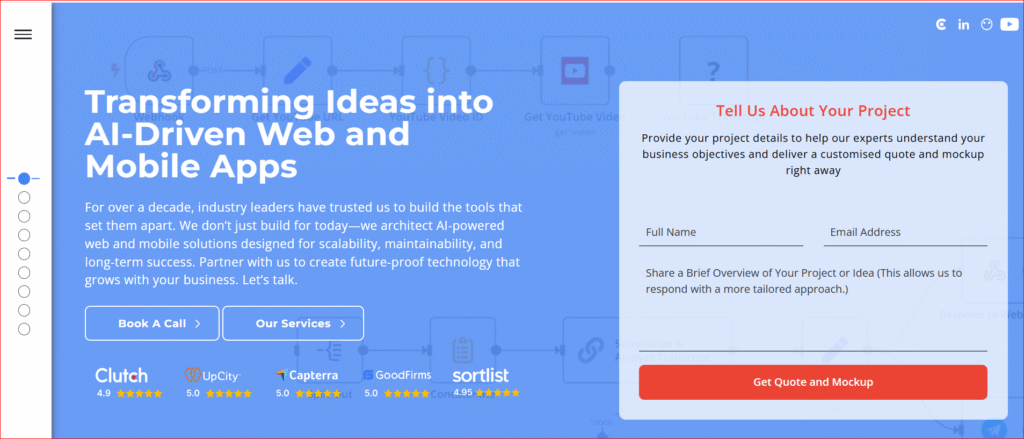
Agile Cyber approaches manufacturing AI with a strong emphasis on cybersecurity and operational technology (OT) protection. Their background in industrial cybersecurity gives them a unique perspective on the security challenges that come with connecting manufacturing systems to AI platforms.
Their manufacturing AI solutions are built with security considerations integrated from the ground up rather than added as an afterthought. This includes implementing secure communication protocols between AI systems and manufacturing equipment, establishing network segmentation to isolate critical systems, and developing monitoring systems that can detect unusual AI behavior. Their expertise extends to helping manufacturers comply with industry-specific security standards like NIST Cybersecurity Framework and ISA/IEC 62443.
7. WillowTree Apps
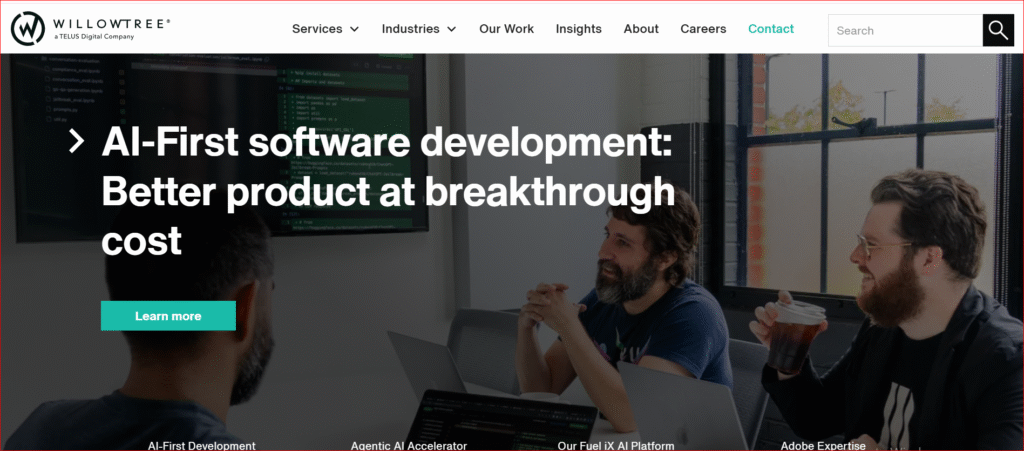
WillowTree Apps brings a mobile-first perspective to manufacturing AI, focusing on creating applications that allow plant personnel to interact with AI systems through smartphones and tablets. Their approach recognizes that modern manufacturing workers expect technology interfaces that are as intuitive as consumer applications.
Their manufacturing applications emphasize usability and accessibility in plant floor environments. Their mobile applications are designed to work with gloves, in bright sunlight or poor lighting conditions, and where users might be distracted by machinery noise. They develop applications that function reliably even when network connectivity is intermittent, storing data locally and synchronizing when connections are available. Their development process includes extensive user research and testing with actual manufacturing personnel.
8. Intermedia IT
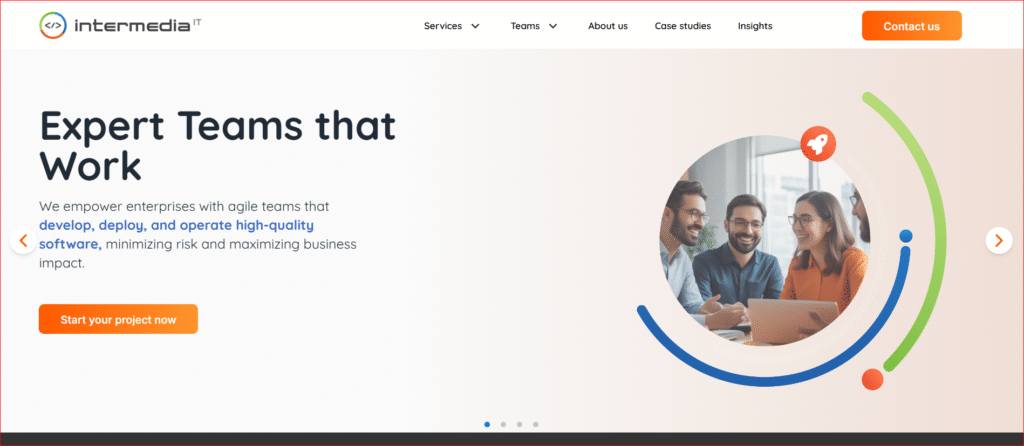
Intermedia IT focuses on the infrastructure and integration challenges that often determine the success or failure of manufacturing AI projects. Their expertise lies in connecting AI systems with existing manufacturing infrastructure, including legacy equipment, control systems, and data sources that weren’t designed to work with modern AI platforms.
Their approach emphasizes practical integration solutions that work with existing investments rather than requiring complete system replacements. They develop middleware and integration platforms that extract data from older manufacturing systems and translate it into formats that modern AI algorithms can process. Their integration solutions often include data historians and real-time databases that collect and organize manufacturing data for AI analysis while maintaining compatibility with existing systems.
9. Streaver
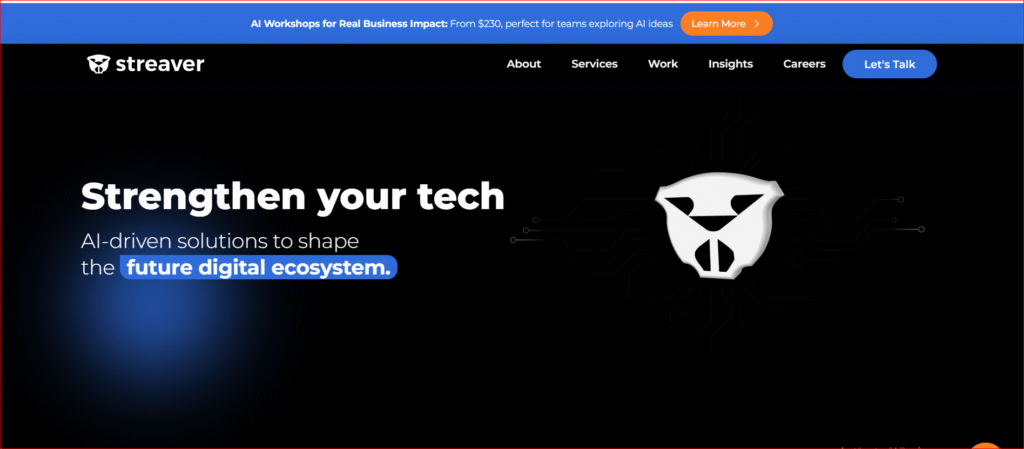
Streaver specializes in developing AI solutions for complex manufacturing processes that involve multiple variables and interdependencies. Their expertise proves particularly valuable for process industries like chemicals, pharmaceuticals, or food processing where small changes in operating conditions can significantly impact product quality, yield, or safety.
Their AI systems excel at analyzing complex process data to identify optimal operating conditions and detect deviations that might lead to quality issues or safety problems. Streaver’s algorithms process multiple data streams simultaneously – temperature, pressure, flow rates, chemical concentrations – to identify patterns and relationships that might not be apparent to human operators. Their team includes process engineers and subject matter experts from various manufacturing industries who understand specific challenges and requirements of different production processes.
10. Code Ninja Consulting
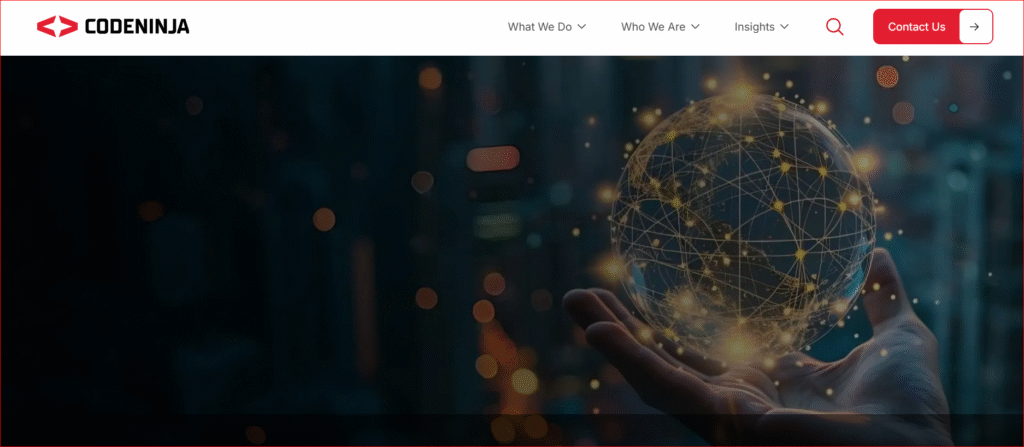
Code Ninja Consulting takes a pragmatic approach to manufacturing AI, focusing on developing solutions that solve specific business problems rather than implementing AI for its own sake. Their methodology starts with understanding the client’s most pressing manufacturing challenges and then determining whether AI is the best solution or if simpler approaches might be more effective.
Their manufacturing practice emphasizes rapid prototyping and iterative development, allowing clients to see AI solutions in action before committing to full-scale implementations. This approach proves particularly valuable in manufacturing environments where the cost of implementing ineffective solutions can be substantial. Their project teams include business analysts who focus on measuring and validating the business impact of AI implementations, developing metrics that track how AI solutions affect key manufacturing performance indicators like overall equipment effectiveness (OEE) and first-pass yield.
Manufacturing AI isn’t just about having the latest technology – it’s about finding partners who understand the unique challenges of your industry and can deliver solutions that work in real production environments. The firms listed here have proven track records of implementing AI systems that deliver measurable results in manufacturing operations.
The key to successful manufacturing AI implementation lies in choosing partners who understand that your primary goal isn’t to have the most advanced AI system, but to improve manufacturing performance, reduce costs, and maintain the reliability that your customers depend on. Look for consultants who speak your language, understand your constraints, and can deliver solutions that work with your existing investments and operational requirements.
Ready to see how AI can solve your specific manufacturing challenges? Schedule a strategy session with our manufacturing AI specialists and get a customized roadmap for your digital transformation journey.
FAQs About AI Consulting Firms for Manufacturing
1. How can AI consulting firms help manufacturing businesses?
AI consulting firms help manufacturers implement smart automation, predictive maintenance, quality control systems, and supply chain optimization using artificial intelligence. They assess your current processes and guide you through AI adoption to boost efficiency and reduce costs.
2. What are the most common AI use cases in manufacturing?
Top applications include:
- Predictive maintenance of machinery
- Real-time production monitoring
- Quality inspection using computer vision
- Demand forecasting and inventory optimization
- Energy consumption and waste reduction
3. Is AI suitable for small and mid-sized manufacturing companies?
Yes. AI is no longer just for large enterprises. Many AI consultants offer affordable, modular solutions that scale with your operations—making it possible for SMEs to adopt AI in phases and see quick returns.
4. What kind of data do manufacturers need for AI implementation?
AI relies on operational data like machine logs, sensor data (IoT), production throughput, maintenance records, and supply chain information. A good AI consultant will help assess and clean your data for effective model training and use.
5. How long does it take to see results from AI in manufacturing?
Initial results can be seen within 6–12 weeks with pilot projects like predictive maintenance or defect detection. Full-scale transformations may take several months but typically result in significant cost savings and productivity gains.